Aiming to Address Energy Challenges through the Development of Catalysts that Minimize Reliance on Precious Metals
Developing Catalysts that Require Minimal Volumes of Precious Metals or None at All
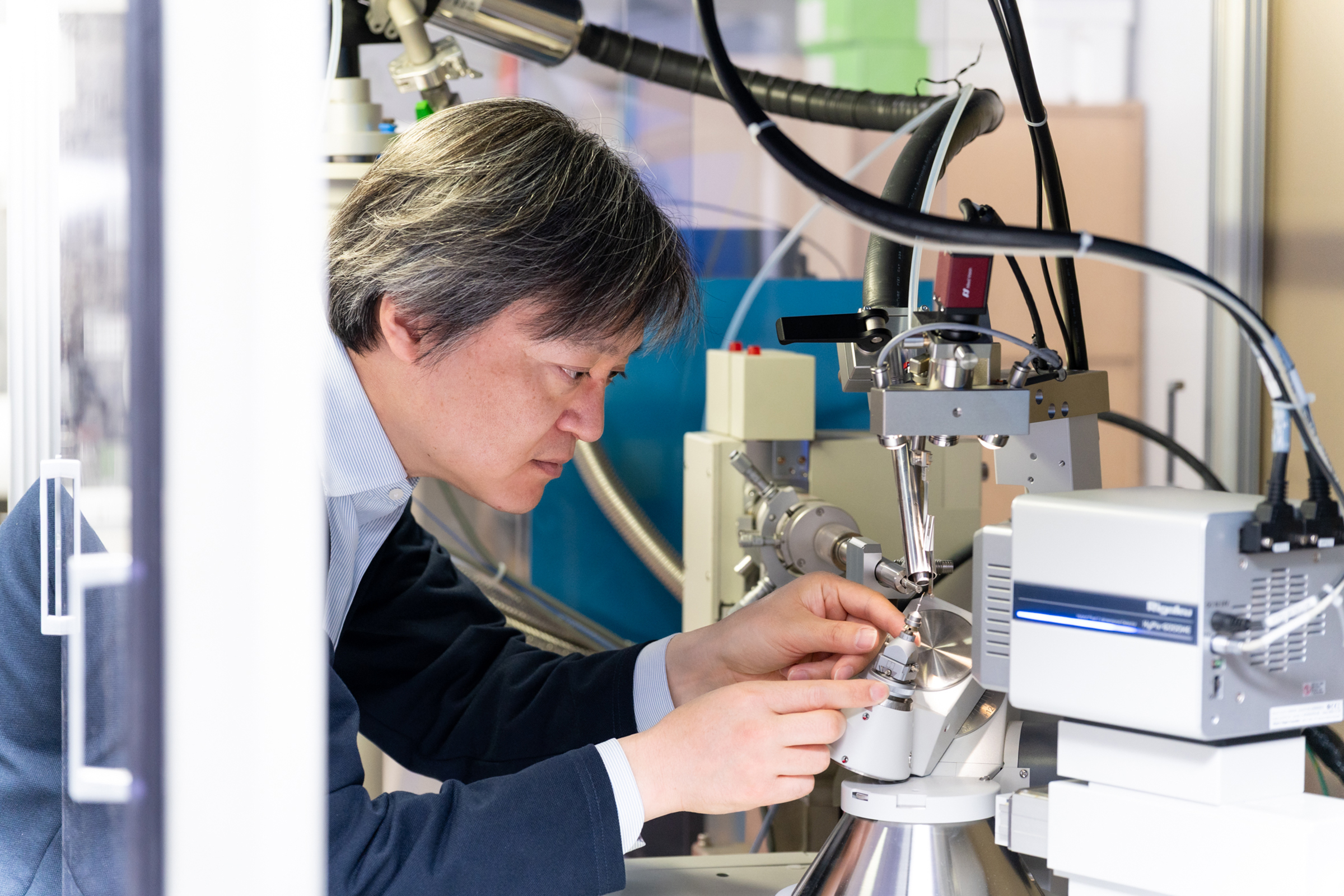
Catalysts that accelerate chemical reactions with a high degree of efficiency are essential in a wide range of fields, from developing raw materials for pharmaceuticals and agrochemicals to producing plastic products. However, as many catalysts rely on relatively expensive and rare precious metals, efforts have been underway to develop alternatives, either by creating catalysts that function with significantly reduced amounts of precious metals or by replacing them entirely with substitute materials. Amid these ongoing efforts, Professor Yusuke Sunada at the Institute of Industrial Science, The University of Tokyo has drawn significant attention for developing two innovative catalysts: one that functions with a far smaller volume of precious metals than conventional versions, and another that requires none at all. Recently, Sunada has been applying his precious metal-free catalyst technology to develop new methods of hydrogen production/storage and transportation. How were these groundbreaking catalysts developed, and what potential might they hold for the future? We sat down with Sunada to find out.
Why Are Precious Metals Well-Suited for Use as Catalysts?
Catalysts play a crucial role in increasing the efficiency of chemical reactions. As an example, consider the reaction in which ethylene (C₂H₄) and hydrogen (H₂) combine to form ethane (C₂H₆) (Figure 1). Ethylene consists of two carbon atoms connected by a double bond, one of which breaks when it reacts with hydrogen. The carbon atoms are then only connected via a single bond, and the hydrogen atoms attach to the newly available bonding sites, resulting in ethane. Professor Sunada explains the role that a catalyst would play in this reaction.
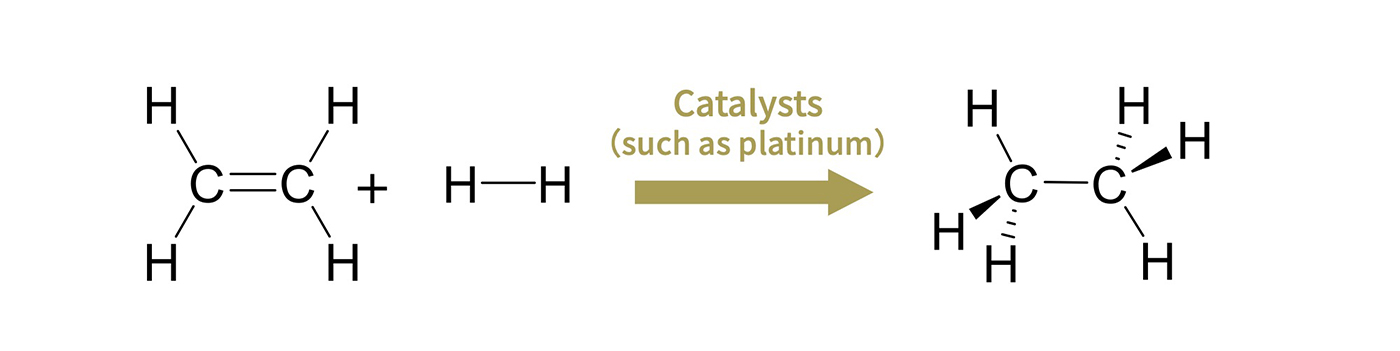
Fig. 1 C2H4 (ethylene) + H2 (hydrogen) → C2H6 (ethane) Precious metals such as platinum are generally used as catalysts. The catalyst itself remains unchanged before and after the reaction and plays a role in the efficiency of the reaction.
Credit: Yusuke Sunada Laboratory
“A catalyst first facilitates a reaction by bringing the ethylene (C₂H₄) and hydrogen (H₂) together in closer proximity. It then breaks the bond between the two hydrogen atoms and weakens the double bond between the carbon atoms in the ethylene. New bonds then form between the ethylene’s carbon atoms and the activated hydrogen atoms, producing ethane. That’s the role of a catalyst—to create a favorable environment for the reaction and to break existing bonds.”
A typical catalyst for this reaction is platinum (Pt), a type of precious metal––a category that broadly refers to rare and relatively chemically stable metals commonly used as catalysts in a wide range of chemical reactions. Breaking existing bonds to form new ones requires the ability to accept or donate the electron pairs involved in bonding. Precious metals such as platinum and palladium possess the necessary properties for this purpose, making them suitable as catalysts.
“However, precious metals are scarce. They’re expensive and quantities are limited. That’s why researchers have been seeking ways to develop catalysts that either make use of no precious metals at all or require only minimal amounts. Yet, no truly satisfactory solutions have been found. To address this issue, we’ve been working to develop two types of catalysts: one that functions with the bare minimum of precious metals, and another that is completely free of precious metals.”
What are these catalysts? Let’s take a closer look at each of them.
Achieving Performance Exceeding that of 10,000 Atoms––Using just Four
Let’s begin with the first type of catalyst, which functions using a minimal volume of precious metals. The ultimate goal, of course, is to eliminate the need for precious metals altogether, but as Sunada notes, there are still cases in which their use is unavoidable. The goal when developing this catalyst was to minimize the volume of precious metals needed when their use is unavoidable.
“Catalysts involving precious metals typically make use of nanoparticle catalysts made up of several hundred to as many as 10,000 precious metal atoms. Such catalysts are widely used in exhaust gas purification and fuel cells. However, when considering the catalytic mechanism, it began to seem possible to achieve catalytic functionality using far fewer atoms because only the atoms on the surface of the particle—those in contact with the external environment—seemed truly essential for catalytic activity. So, I decided to try creating a material with only a few precious metal atoms arranged in a flat planar structure, as if slicing off a portion of the particle’s surface.”
However, when it came to actually creating it, arranging metal atoms into a flat planar structure proved to be extremely difficult. To overcome this, Sunada adopted a silicon compound featuring multiple single Si-Si bonds to serve as a structural template, into which he attempted to embed metal atoms between the Si-Si bonds. This enabled him to successfully arrange palladium atoms in a flat planar structure. The resulting material featured three silicon atoms and four palladium atoms in a perfect hexagonal plane. Astonishingly, tests of its catalytic performance showed that it matched—or even exceeded—the performance of nanoparticles made up of thousands of palladium atoms.
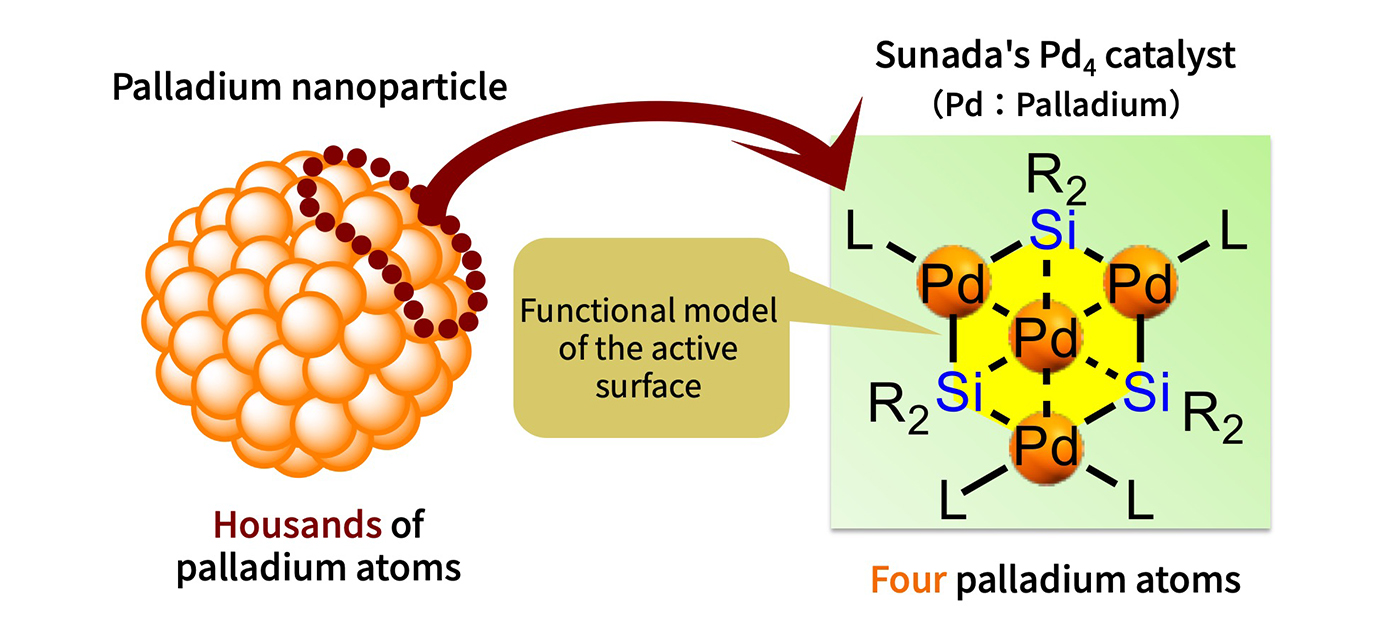
One part of the surface of nanoparticles consisting of a few thousand precious metal atoms (palladium) can be regarded as approximately planar. To create such a planar material with palladium, a silicon compound was used as a “template”, and the compound shown on the right was synthesised.
Credit: Yusuke Sunada Laboratory
“When compared based purely on the number of palladium atoms, the new catalyst was roughly 1,000 times more efficient. It was a truly astonishing result. Additionally, deeper exploration into how just four atoms could deliver catalytic performance equal to or greater than that of several thousand revealed the importance of silicon. It seemed that the silicon used as the structural template was playing a crucial role.”
What exactly does this mean? The answer lies in another key area of Sunada’s work, namely, his research into developing a catalyst completely free of precious metals. Let’s take a closer look into this groundbreaking line of study.
A Precious Metal-Free Catalyst Using Silicon and Iron
Sunada had been working to develop a catalyst without use of precious metals long before beginning to search for a catalyst requiring a minimal volume of such metals. Over a decade ago, a student in his lab made a pivotal breakthrough in this research. They discovered that a their newly synthesized compound combining silicon and iron could deliver catalytic performance comparable to that of precious metals. The compound even eliminated the need for precious metal catalysts in chemical reactions that had previously required them, such as in synthesizing materials for use in silicone products.
“Iron isn’t intrinsically very good at breaking chemical bonds, but we found that when placed next to silicon, it gains that ability. Silicon enhances iron’s catalytic performance by influencing its electronic state and expanding its role as a reactive site, boosting the reactivity of the iron. Silicon seems to play a similar role supporting palladium in the minimal precious metal catalyst mentioned earlier.”
Even before beginning this line of research, Sunada had taken an interest in silicon’s similarities to metals, despite not being a metal itself, and over the course of multiple studies he explored combining silicon with various metals. He describes his use of silicon in this way as his “greatest act of originality,” and indeed, it proved to be the crucial key in developing both the minimal precious metal and precious metal-free catalysts.
Studying Catalysts to Help Address Energy Challenges
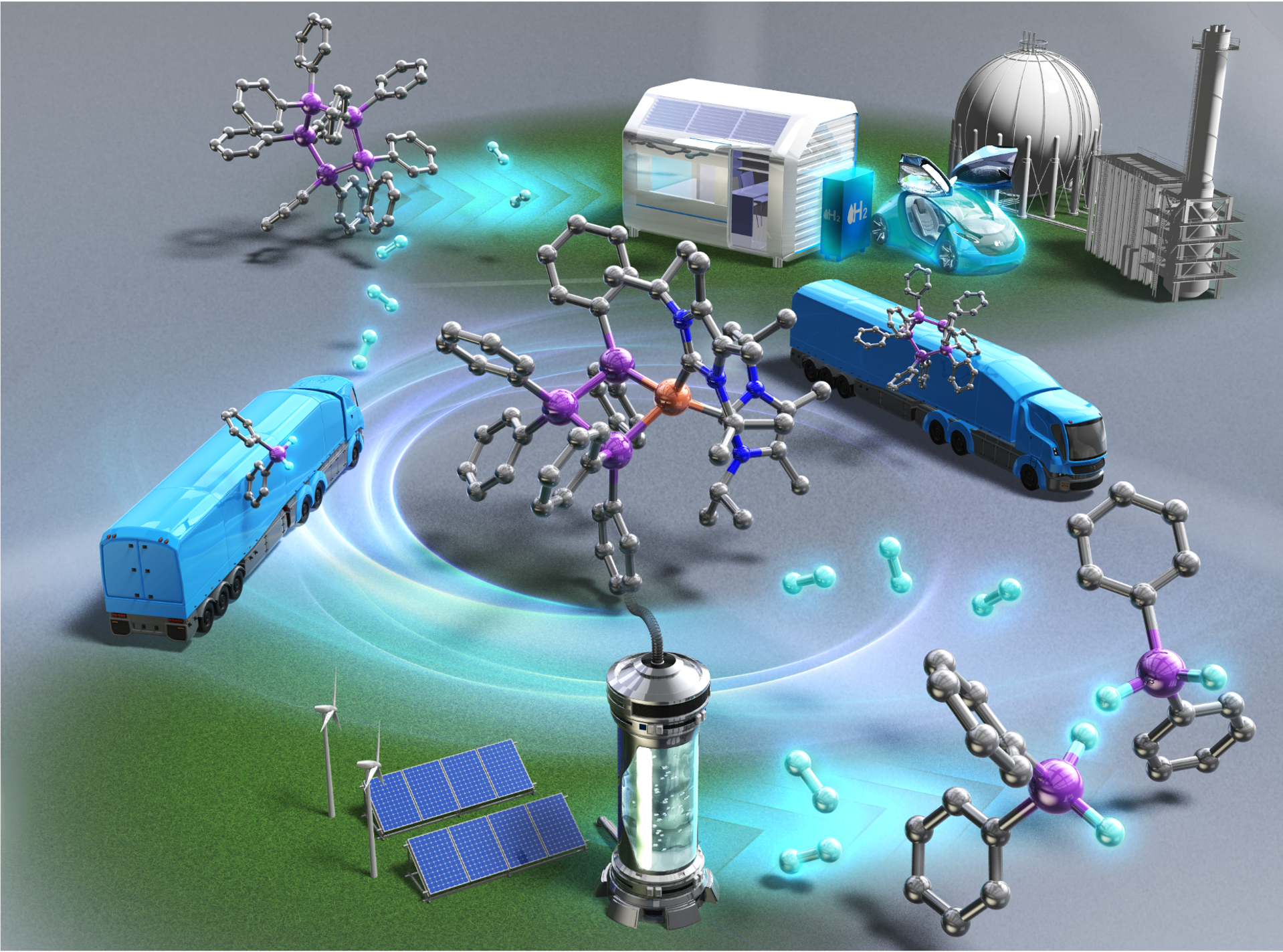
Chem. Sci., 2023, 14, 1065 (cover picture)
Precious metal-free catalysts have a wide range of potential applications. Among them, Sunada is currently focusing on applications relating to hydrogen. In particular, he aims to develop new methods for production, storage and utilization of hydrogen—which shows promise as a next-generation energy source—by leveraging precious metal-free catalyst technologies.
Ensuring the widespread adoption of hydrogen will require the development of safe and energy-efficient means of production, storage and transportation. One approach of particular interest to Sunada involves storing hydrogen in the form of chemical bonds within chemical compounds. The most extensively studied example of this at the present time involves the use of the organic compound methylcyclohexane (MCH), in which hydrogen is stored within carbon-hydrogen bonds and can be released as hydrogen gas by breaking those bonds. Sunada is working to develop a method based on the siimilar approach, using a precious metal-free catalyst to enable a more energy-efficient and sustainable form of hydrogen storage.
“Our method stores hydrogen in a compound formed by bonding hydrogen with germanium, which belongs to Group 14 of the periodic table, just like silicon, and shares many of its chemical properties. To make it possible to release and absorb hydrogen from this compound, we use a combination of iron and germanium as a catalyst during the reaction. This approach enables the release and storage of hydrogen at room temperature, all without the need for precious metals. Conventional methods using MCH require heating to around 300°C to release hydrogen gas. If this can be achieved at room temperature, it would offer a major advantage in terms of energy efficiency.”
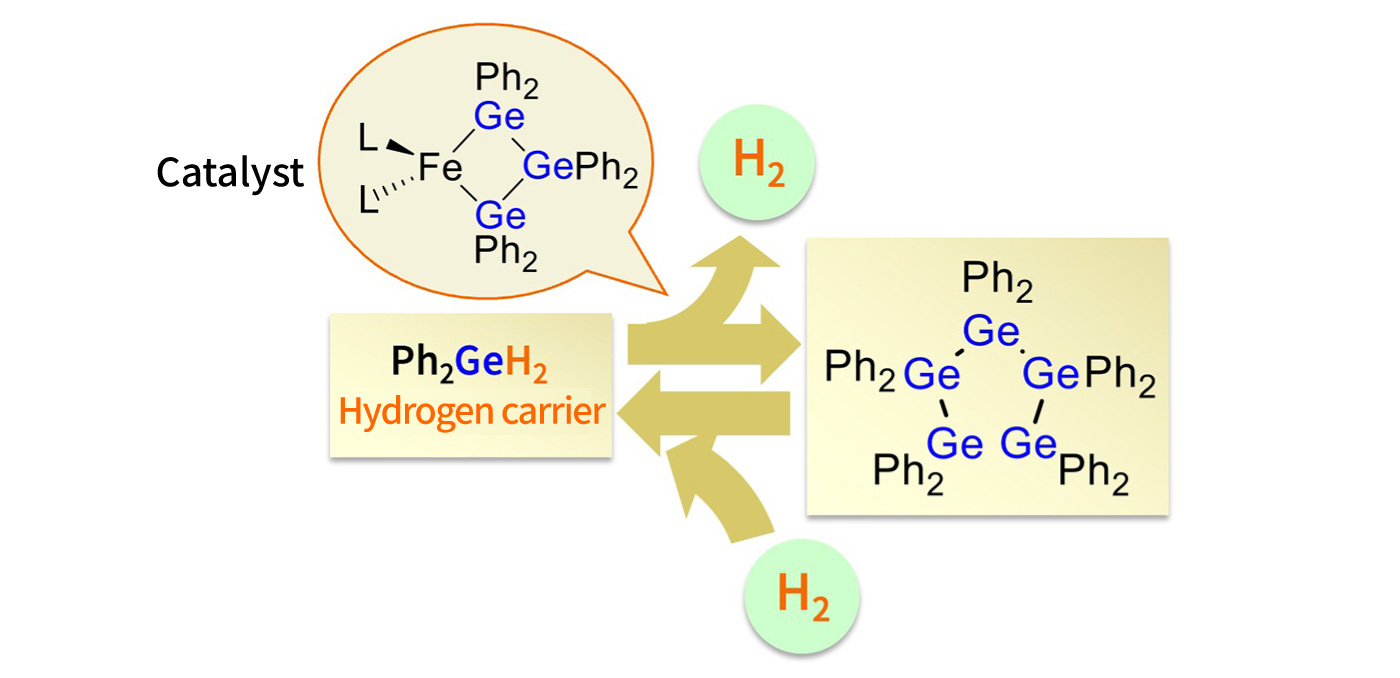
A compound of germanium (Ge) and hydrogen (Ph is a phenyl group (C6H5)) is used as a hydrogen carrier to store hydrogen. A rightward reaction allows hydrogen to be extracted and a leftward reaction allows hydrogen to be stored. As a catalyst for the reaction, a “precious metal-free” compound of iron and germanium is used. However, germanium is expensive, so Sunada is currently developing a method using silicon instead. Silicon requires slightly more heating to generate hydrogen, but still saves a considerable amount of energy compared to 300°C.
Credit: Yusuke Sunada Laboratory
Sunada and others in his group have already succeeded in developing this method and are now working to make it available for practical applications. The journey ahead is unlikely to be a short one, but as Sunada puts it, “Even in the face challenges, steady research always opens up new paths, and I truly enjoy the day-to-day process of trial and error alongside my students.” Beyond that, what other possibilities does the future hold? Looking ahead to the future that this technology could help shape, Sunada commented as follows.
“The scope of catalyst technologies and their underlying principles are not limited to specific targets like hydrogen. Even if, moving forward, ammonia is seen as a more practical energy source than hydrogen, the outcomes of our research will likely be just as applicable. We intend to continue building up research that is meaningful on a fundamental level. And it would be truly rewarding if our work can someday contribute to addressing the energy challenges that we all face.”
Yoshinao Kobayashia and Yusuke Sunada, “Germanium hydrides as an efficient hydrogen-storage material operated by an iron catalyst”, Chemical Science(2023), DOI: 10.1039/D2SC06011F
Related Article> “Butterfly-Shaped” Palladium Subnano Cluster Built in 3-D
Comments
No comments yet.
Join by voting
How did you feel about the "Possible Future" depicted in this article? Vote on your expectations!
Please visit the laboratory website if you would like to learn more about this article.
Share